Metal bending is a process in which the metal is deformed by applying force to a part of it, which makes it bend at a certain angle and obtain the desired shape. The place of force on the metal sheet and its amount are calculated in the design stage. Paying attention to some important points in the design allows us to bend the sheet in such a way that it looks exactly like the desired design.
🔲 Minimum flange length
The minimum flange length is one of the important points in the field of bending design. This factor is calculated according to the thickness and width of the mold. If you design a flange that is too short, it will uncomfortably create a gap in the sheet and you will not achieve the desired result.
🔲 45 degree lathe
The 45 degree turn must be stopped before the partial base is reached. If you want to make a flange with one or both ends chamfered to 45 degrees, the previous tip regarding minimum flange length still applies. 45 degree lathes must provide enough space to make proper bends, otherwise unpleasant deformation will occur.
🔲 Distance from the hole to the bend
Holes close to the bend may be twisted. If the holes are too close to the bend, they may become deformed. Round holes are not as problematic as other types of holes, but screws may still not come out. You should pay attention to the dimensions of the bending force to measure the minimum flange, so that the holes have the minimum distance to each other.
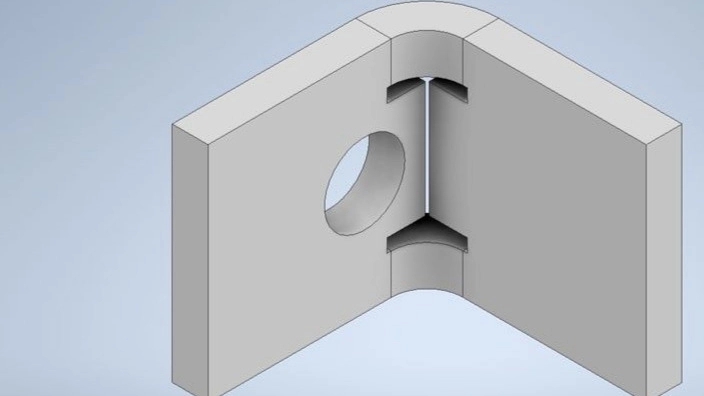
🔲 Symmetry
To avoid confusion and complexity, the rectangular hole can be on both sides of the sheet. Making almost symmetrical parts is risky. If possible, the sheet should be symmetrical. If the sheet design is almost symmetrical, the press bend operator may get confused and bend the desired sheet in the wrong direction. Symmetry cannot be guaranteed in every design. You must be sure that it is easy to give the machine accurate parameters for symmetrical design.
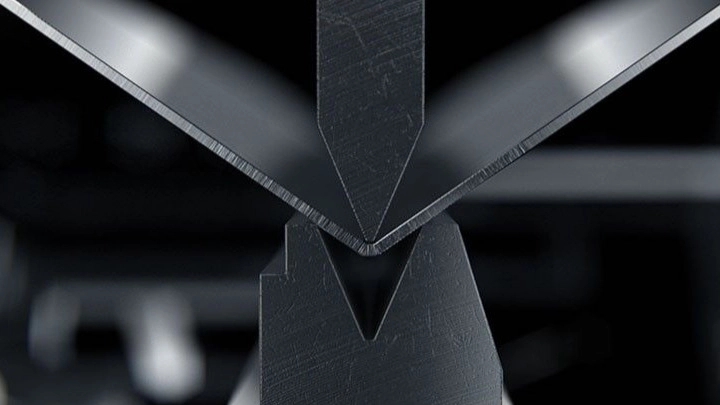
Riveting the beads
This point becomes important in bending the tool. If you are using riveted nuts near the bend line, it will obviously be beneficial to insert them before the bend to ensure serviceability. After bending the sheet, the holes may change shape. However, when bending, be sure that the nuts do not prevent the tools from working.
🔲 Small flanges in large parts
A small bend at the end of a large part may lead to problems. It is better to remove small flanges with large and heavy parts. This makes the production of bent sheet very difficult and may require manual intervention. But it will cost more than simple machining. As a result, it is better to choose an alternative solution if possible.
🔲 Bends that are placed next to each other
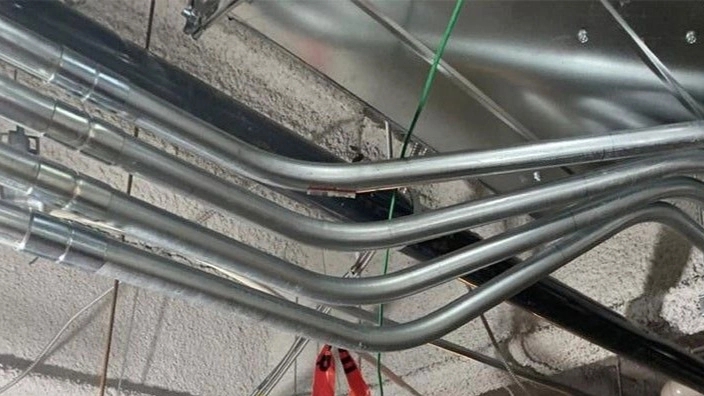
First, the amount of bending force corresponding to the minimum length of the flange should be obtained. Before making bends next to each other, you should make sure of the capability of the metal sheet and your design. You may have a problem when you want to place the bent part on the mold. If your bends are in the same direction, such as a U-bend, a common design rule is to design the middle section to be longer than the flange.
🔲 Keeping the bends in one line
Having a large number of bends in the design requires a lot of adjustments. It is better to keep the bends in one line if there are several flanges in a row. With this account, you can minimize the number of operations. Otherwise, the operator must readjust the parts for each bend, which means more time and cost.
🔲 Bending line parallel to one side of the metal sheet
Non-parallel bending lines lead to incorrect results. As mentioned, the bend lines must be parallel to one side of the sheet metal for positioning. Otherwise, aligning the sheet will be a real headache and an undesirable result may be obtained.
🔲 Prominence of bending
Highlighting the bend is essential. To get the best result, it is necessary not only to make a small laser cut, but also to make an actual cut on the sides of the flange, so that a ridge is obtained in the bend. The width of such a cut should be greater than the thickness of the material. This ensures that there will be no tearing or deformation in the final bend. Another good practice with this design is to add small radii to the bend ridges, as they reduce the stresses on the sheet.
Bending a box
Small gaps ensure a practical job. When bending the box, small gaps should be left between the flanges. Otherwise, the last bend can collide with the existing screws and break the whole structure.

🔲 Checking the flat pattern
One thing to keep in mind is to change your CAD view to a flat model from time to time. There are many advantages in this method. First, if you deviate from your flange, you may end up with a design that cannot exist flat. What cannot be found in a flat pattern, will not be found in any other pattern.
Measure the layout. You may be able to adjust the design for a better fit. If a smaller size is applicable, avoid going to a larger sheet. Maybe if you cut a few millimeters off the design, you can fit 2 pieces on one sheet. This action affects the final price.
🔲 General rule for minimum bending radius
Choosing the inner radius of bending according to the thickness of the sheet is one of the simplest tasks in the design of metal sheet bending. Choosing the right value of the bending radius will prevent future problems. If the value of the bending radius is less than the appropriate value, it will cause many problems in the next steps. If the radius is chosen larger than the appropriate one, it makes the next calculations difficult.
Bending direction
Bending direction should be perpendicular to the sheet. The bends should not be parallel to the design of the sheet. This is especially important in the case of aluminum and hardox.
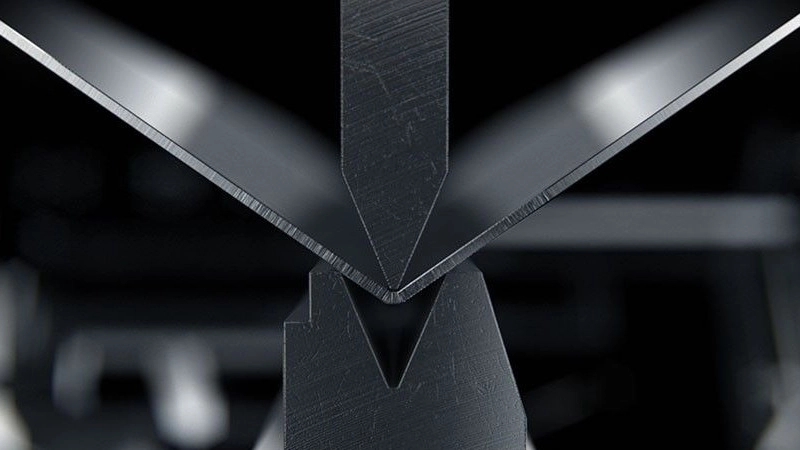
🔲 Edging
Include an inner radius in your design if possible. If you want to reinforce the edges of your sheet metal, edging is a great option. However, some recommendations should be considered. It is better to leave a small radius inside the sheet.